Mineral casting CNC machines are notable for their use of a composite material, typically consisting of mineral aggregates and resins, to create the machine’s base and components. This design offers several advantages:
Benefits:
- Vibration Damping: Mineral casting has excellent damping properties, reducing vibrations during machining, which enhances precision.
- Thermal Stability: The material maintains dimensional stability over a wide temperature range, helping to keep tolerances tight.
- Durability: It resists wear and corrosion better than traditional materials like cast iron.
- Customization: Mineral casting can be molded into complex shapes, allowing for innovative designs in machine structure.
- Lower Weight: Compared to some metal counterparts, mineral casting can be lighter, making it easier to handle and transport.
Applications:
Mineral casting CNC machines are used in various industries, including:
- Aerospace: For high-precision components where accuracy is critical.
- Automotive: In manufacturing complex parts that require tight tolerances.
- Medical: For producing precision instruments and devices.
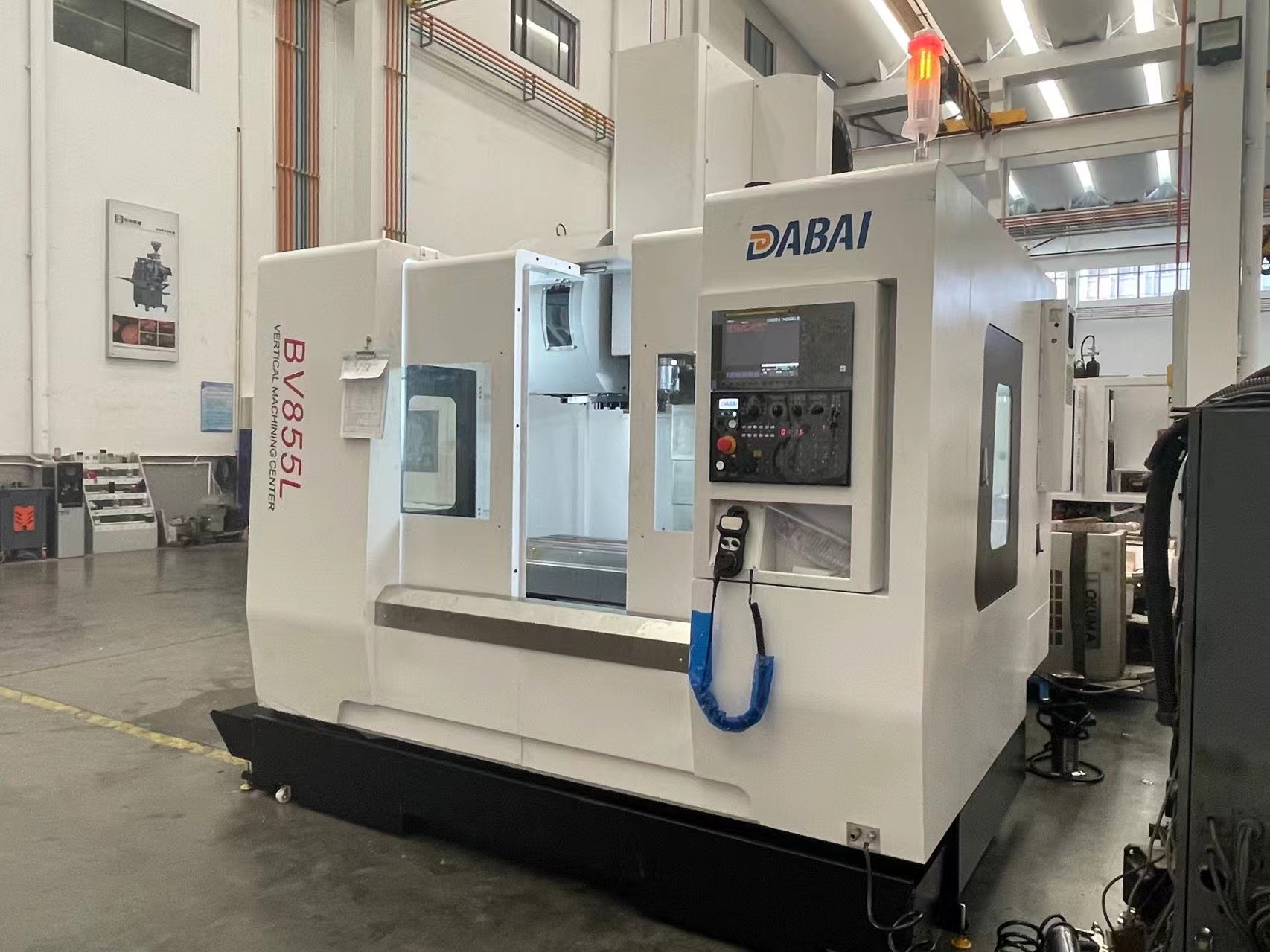
Considerations:
When selecting a mineral casting CNC machine, consider factors such as:
- Size and Work Envelope: Ensure the machine fits your operational needs.
- Control Systems: Look for user-friendly interfaces and advanced control capabilities.
- Maintenance: Evaluate the maintenance requirements for the machine and the material.
Overall, mineral casting CNC machines are an excellent choice for applications demanding high precision, stability, and durability. If you have specific questions or need more details, feel free to ask!
www.dabaicnc.com